University of Toronto’s Professional Experience Year (PEY) Co-op program is a work-integrated learning program that helps engineering undergraduate students gain paid work experience before they graduate. For 14 months, I had the opportunity to work at Toyota Canada as a quality engineering intern. My main areas of responsibility were the following:
- Carried out root cause analysis and countermeasure development on accessory quality concerns,
- Lead and managed projects that evaluated new potential products on safety, compliance, and feasibility,
- Reviewed engineering drawings and quality control reports,
- Performed warranty analysis to assess warranty trends and to identify areas for continuous improvement, and
- Processed warranty claims to recuperate warranty services performed at dealerships nationwide.
Achievements & Highlights
By leveraging SAP and Excel VBA to automate warranty claim processing, more than $200,000 was recuperated, which is more than double the amount compared to the year prior. Total of 21 quality cases were resolved by working with suppliers and development engineers to test accessory parts for failure verification, for failure duplication, or as part of an internal investigation to resolve manufacturing and design related issues. In addition, 2130 unique part numbers were analyzed and warranty trends were identified to proactively tackle quality issues on various Toyota accessory products.
Some of the notable quality tests performed are the following:
- Tested engine block heaters in high thermal settings (i.e. during regular engine operation and in high heat ovens) to measure the durability of the wire jackets that insulate and protect shielding and center conductor (see Figure 1),
- Installed warranty claimed long-range remote engine starter ECUs, antennas, and remotes in demo vehicles to identify the root cause of failure and to verify warranty claims, and
- Installed dash cameras in demo vehicles to verify the voltage supplied to the dash camera during ignition is above the minimum voltage threshold for proper software boot-up (see Figure 2).
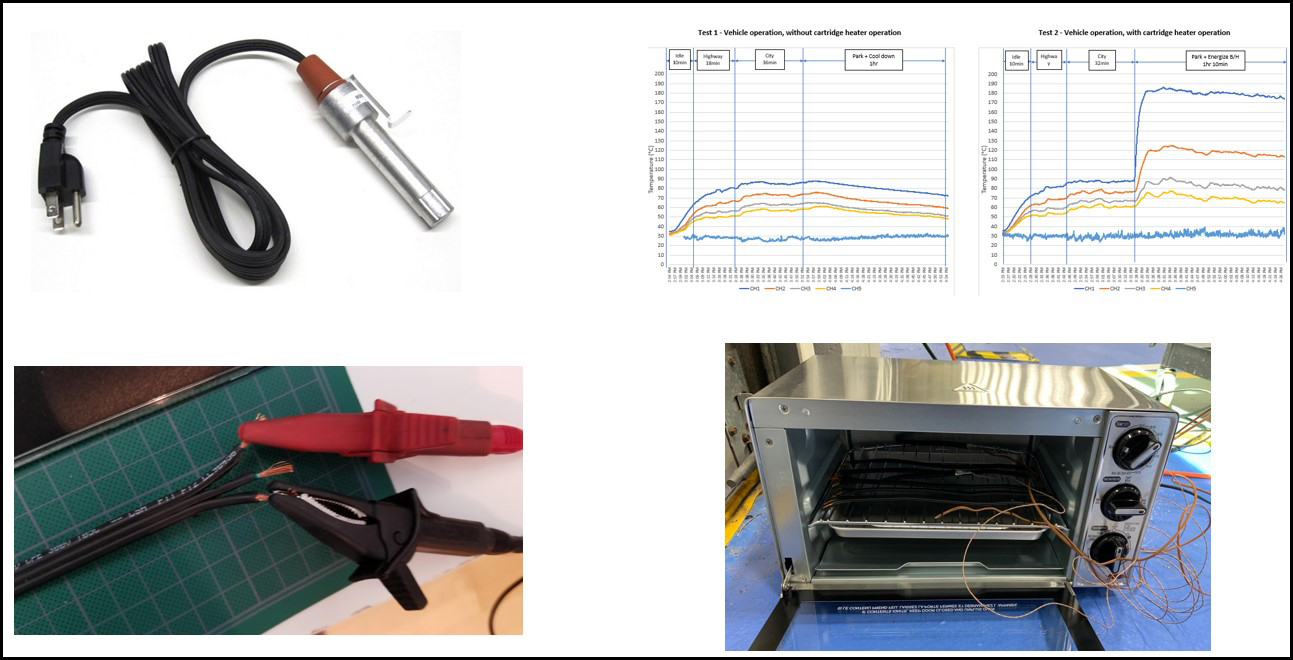
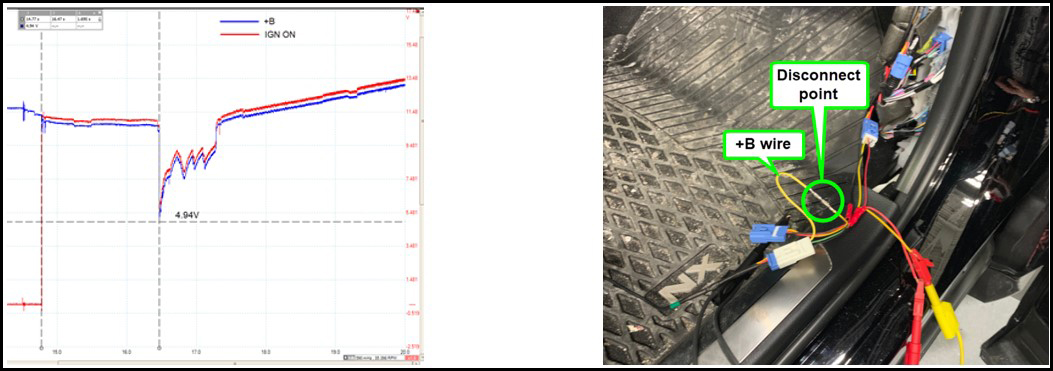
Once quality cases were evaluated and tested, repair manuals (Figure 3) were created and issued to dealerships. Demo vehicles were used to install the accessory relevant to the quality case at hand.
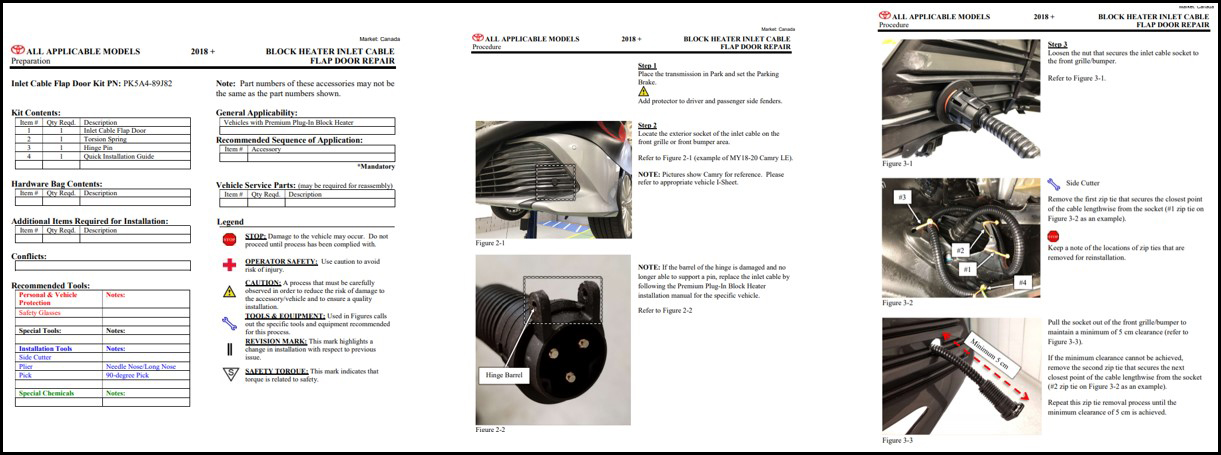
All components and accessories installed in a vehicle have a certain amount of inherent risk that can impact the customer experience and/or the performance of the vehicle (i.e. risk of corrosion, deterioration, overheating, and etc.). Although the level of risk was initially assigned to the categories of the accessory components, they were not individually assigned to each part name and number. This made it difficult to search the risk level of a specific accessory. Therefore, I developed an accessory risk rank search tool program (Figure 4) using VBA that can identify the risk of a specific accessory based on its category, part name, or part number.
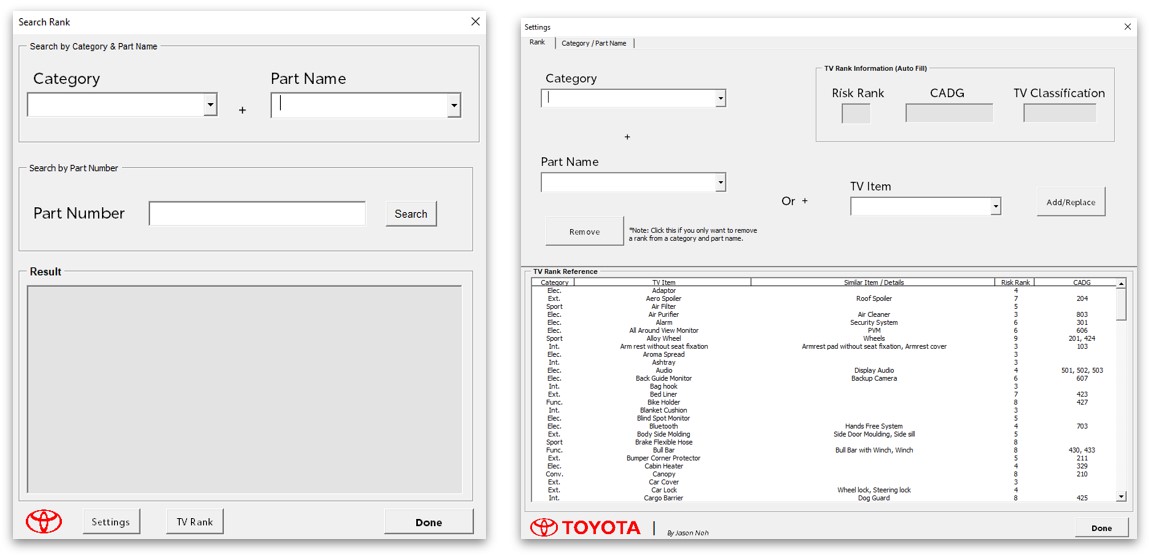
In addition, I had the opportunity to take part in two Toyota University courses:
- Automotive Electrical 2 – Learned to read electrical wiring diagrams and perform diagnosis on electrical components
- Engine Management 1 – Learned engine management related components, maintenance, and basic diagnostic tasks
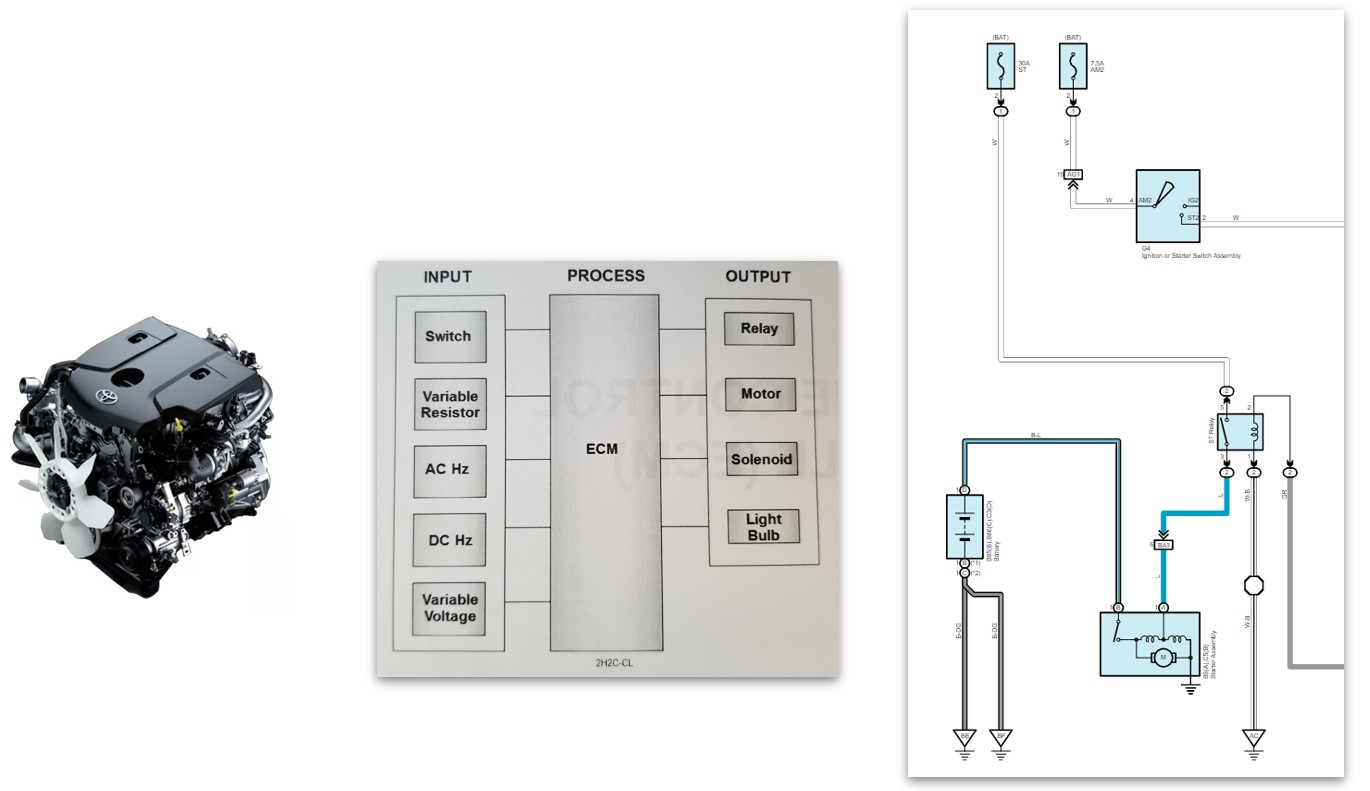
Career Impact
The biggest takeaway that sums up both the technical and soft skills I was able to gain from this internship at Toyota Canada is The Toyota Way – a set of principles that consists of two key areas: continuous improvement and respect for people. I had the opportunity to deeply internalize the importance of identifying and addressing the root cause of problems, driving organizational learning, implementing the right processes to produce right results, developing the people around you, and thinking long term.
Through this experience, I plan to continue to learn, explore, apply this knowledge in a wide range of companies and industries. Moreover, I aim to seek continuous improvement (Kaizen) for myself and others around me, go and see (Genchi Genbutsu) for myself to thoroughly understand any given situation, and (most importantly) always identify, clarify, and investigate the root cause of a problem before seeking a solution.